今回ご紹介する事例では、Formula1などのレースで実際に行われている事例をご紹介します。CAEによる最適化を使用して開発しているフロントのフレキシブルウィングです。みなさんフレキシブルウィングというものをご存じでしょうか?
この事例ではフレキシブルウィングの設計についてご紹介します。
走行風によるダウンフォースを受けると、ウィングが大きく倒れることで抵抗を低減かつ、グランドエフェクトを増大しダウンフォースを稼ぎながら最高速を上昇させる機能を持ちます。こちらのWebサイトが詳しいです。→https://jp.motorsport.com/f1/news/banned-how-formula-1-outlawed-flexi-wings/4804197/
GRMではこのフレキシブルウィング開発に深く関わってきました。Racecar Engineeringの記事(https://www.racecar-engineering.com/articles/flexible-wings-in-formula-1/)を見ていただければわかるように規制ギリギリの性能を狙っています。(GRMの名前が記事内に出ていますね)
フレキシブルウィングを規制するためにFIAによる剛性試験がルールブックに載りました。ウィングの一部を特定の荷重で押した際の変位量を規制されています。
そこで考えられたのが、「FIAの剛性試験はパスできるが、走行風では大きくたわむ」という性能です。CFRPならではの解決策です。CFRPは異方性材料のため「A部への入力には強く / B部への入力には弱く」という制御をすることができる材料です。目標性能と最適化結果は以下のようになりました。
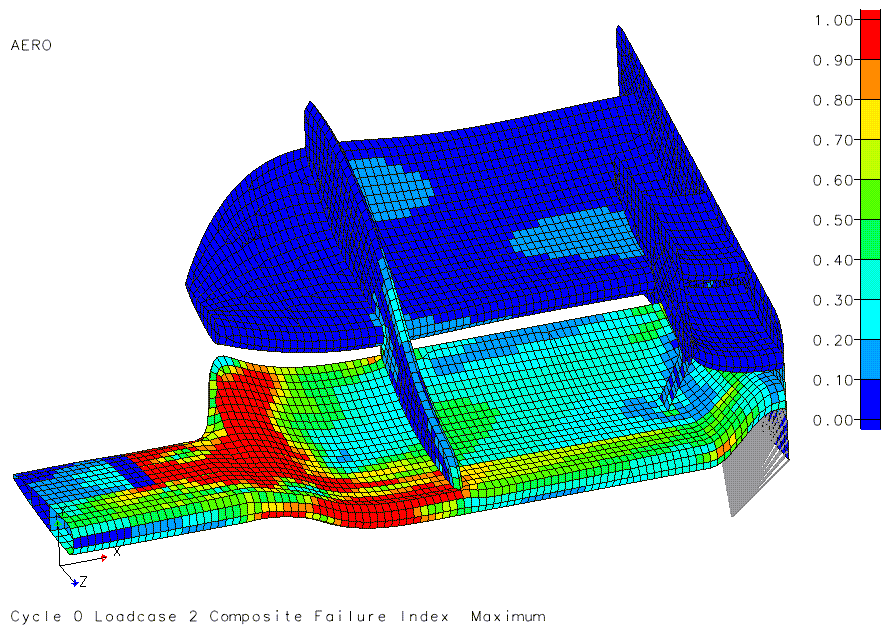
上記CAE結果のカラーコンターは破壊指数を表示しています。ウィングをたわませるためのクビレ部分に大きな範囲で1.0に近い破壊指数になっていることがわかります。
・剛性試験での変位:小(FIA基準クリア)
・走行風での変位:大(車両要求を満足)
複数の荷重条件に対してCFRPの積層を設計するのは設計変数が多すぎるため非常に大変(というか不可能)ですが、CAEによる最適化を使用すれば剛性や強度のコントロールが容易です。
下図は最適化前の初期設計状態と、最適化後計状態の変位比較です。最適化後モデルは大きく後傾することがわかります。

今回の事例では、GRMで行った実際の事例紹介をすることができました。(残念ながら日本国内での事例ではありませんが・・・)
CFRP積層設計のように設計変数が膨大であったり、相反しそうな条件設定など、机上計算では不可能な設計がCAE最適化によりスムーズに行える良い事例だと思います。
また、CFRPは軽量化だけでなく、剛性特性をコントロールできるというメリットが活かされた事例です。
GRMでは過去に様々な製品をCFRPに材料置換してきました。日本では、国内製造メーカーと協業して様々なプロジェクトに参画しています。CFRP製品開発にお困りの際はお気軽にお問い合わせください。
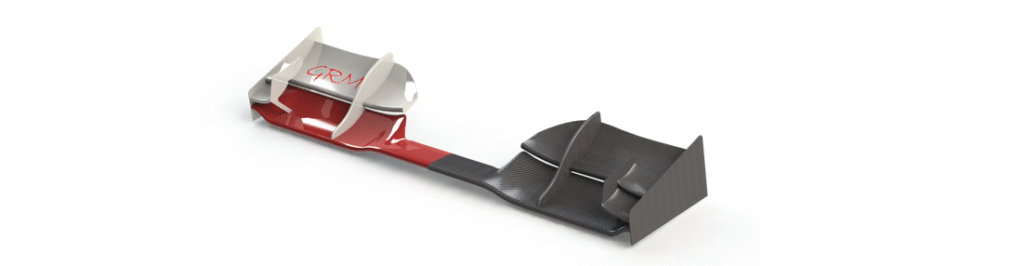