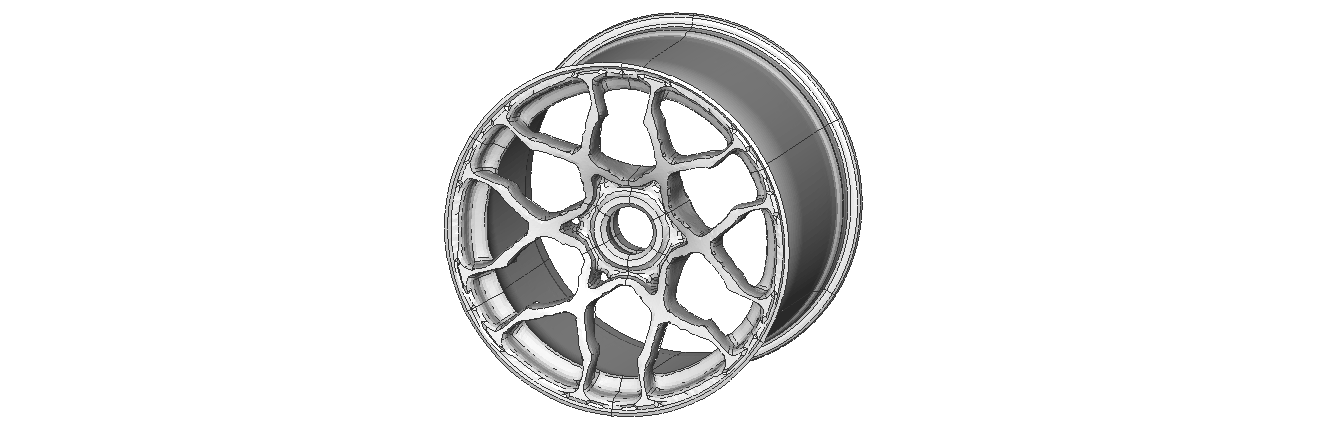
今回の事例では、ホイールを使用したトポロジー最適化のテクニックについてご紹介します。
使用するホイールはセンターロックタイプのホイールにしてみました。余談ですがセンターロックナットは600Nmを超えるトルクで締結する必要があり、公道走行用モデルでは脱落防止用のロックナットを使用しているなど、とても管理が大変なホイールのようです。
設計空間は以下のようにしました。グレー部分(ハブとリム)が非設計空間となり、色付きのスポーク部分を最適化してみます。
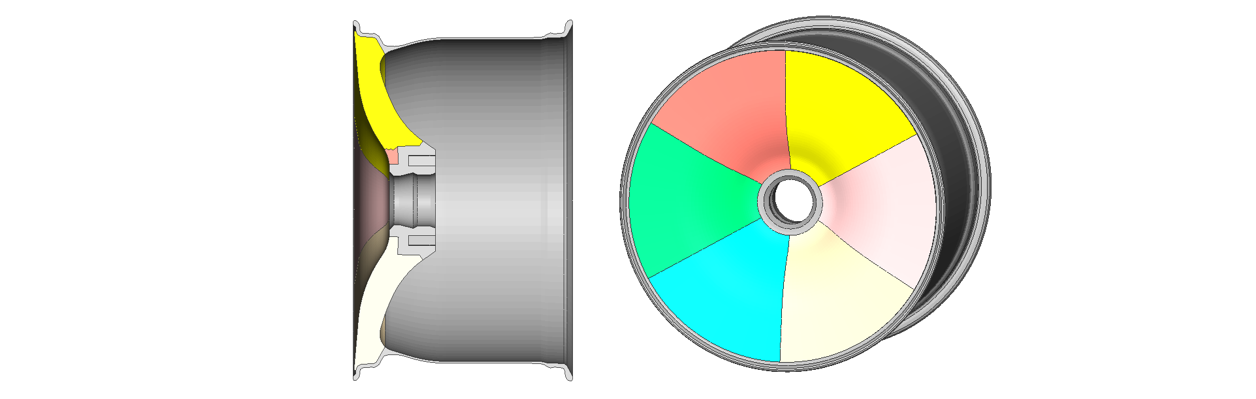
この設計空間作成でのトピックは、
- 狙いのスポーク数になるようにあらかじめ6分割している
- 非設計空間を別のパートIDに分けている
の2点です。以下のようにスポーク形状を作成できる条件設定も可能ですが、事前に分けた方が結果的に良い結果かつ早く計算できる傾向にあります。

なお、設計空間を6分割したのは、私が6分割パターンのホイールが好きという理由だけで、特に意味はありません。
6分割したパターンは、クローニング条件を設定するため全く同じ形状になります。つまり、ホイール全周に荷重条件を設定する必要がありません。
設定する荷重条件は以下の3種類(複数位置)です。
- 上方向への突き上げ荷重相当
- 左右方向への横G相当
- 前後方向への加減速G相当
最適化では、求める車両特性に合わせて剛性を指定したいところですが、本事例とは関係が無いためMF(マスフラクション:設計空間中のどのくらいの材料が残るか)を拘束条件として計算します。
最適化の目的関数は剛性最大化とします。
いくつかのパターンで実施したので結果を見てみましょう。
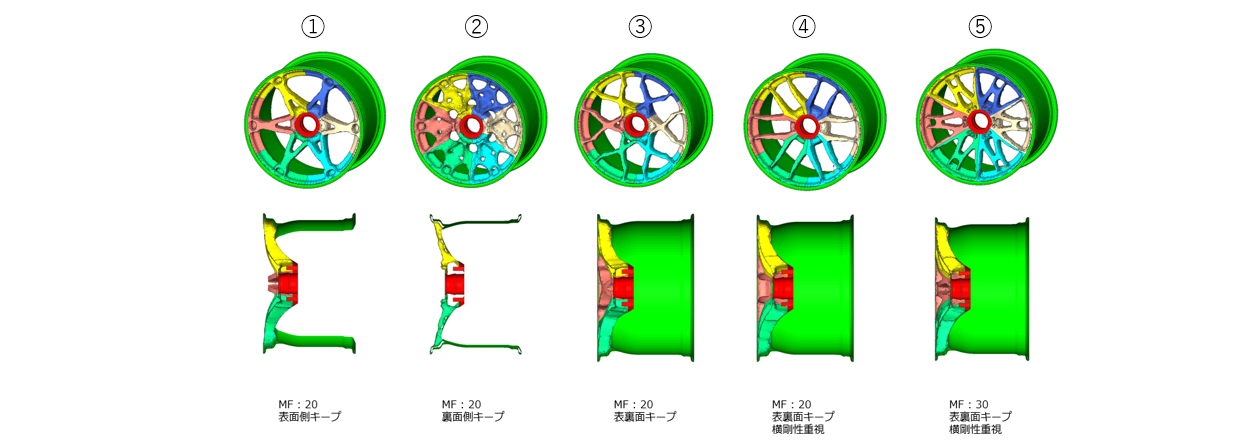
いくつか条件違いを計算した中で、特徴的だった5結果が上記です。
①:スポークとリムの繋がる部分に肉抜きがありかっこいいです。表面基準として、内外両方向へ肉が残る鋳造(鍛造)条件です。
②:スポーク裏面側を基準にしたため、逆ゾリと言われるような形状です。古い車によく見られるようなデザインですね。
③:①と非常に似た条件ですが、アクスル方向への押出条件を設定しています。
④:③をベースに横方向の剛性を優先しました。よく見るYスポークのホイールです。私の車はほぼこの形の純正ホイールです。
⑤:④と同条件で、MFのみ多めにしたものです。MFを変更したことで基本スポーク形状が全く違うところが面白い部分です。
この結果から、③をベースにレビューしてみましょう。
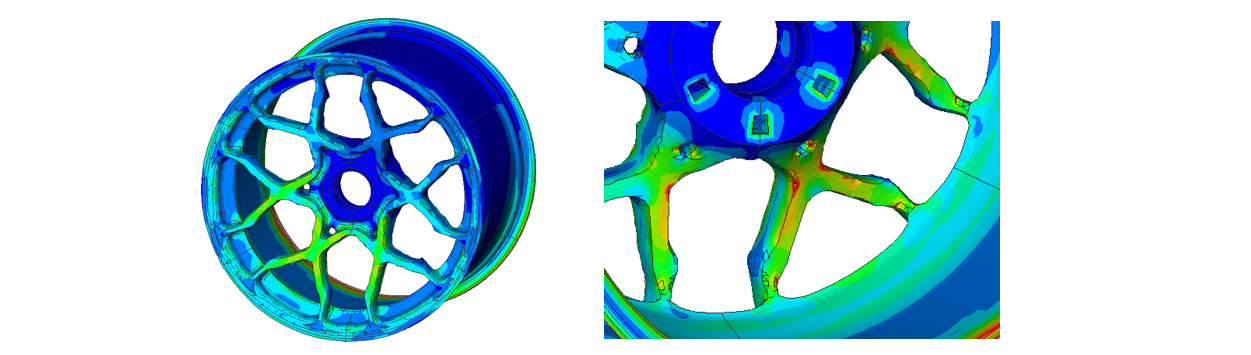
画像は、前画像の黄緑部分のスポークに着目した荷重条件の応力結果合成コンターです。TET10で計算しています。
十分に応力が低い状態ですが、最適化直後のため凹凸により少し応力集中が見られます。スポーク裏側から見てみると、スポークがクロスする部分に微妙な応力集中が見られます。
通常の開発では、この時点でCADによる3D作成をするため上記は3D作成時に修正可能です。
すでにこの状態で、とても軽く、十分な剛性があり、疲労を考慮しても十分に低い応力である状態です。
今回は、形状最適化を使用して応力集中の緩和および駄肉部を削ります。(本来であれば3D作成後がお勧めです)
通常の開発でも、CAD3Dデータからの性能確認解析後、形状最適化でチューニングすることをお勧めします。意匠性や他の要求仕様のために形状変更をするので、上記のように応力集中や駄肉が残りやすいためです。
以下は先ほどの応力確認モデルをさらに形状最適化(Shpae morphing optimisation)を実施した結果です。
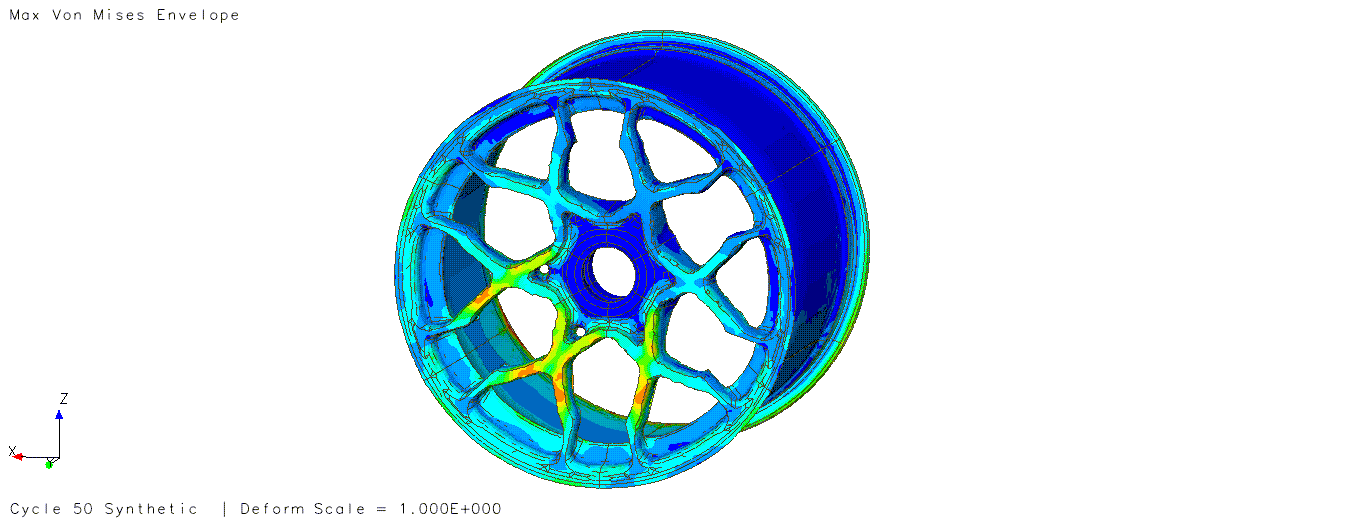
カラーマップは応力コンターを示します。アニメーションは形状変更を示します。スポークの表面側が薄くなり、裏面側が厚くなる様子がわかります。
下図では、以下2つのモデルの応力コンターを示します。(カラースケールは同じです)
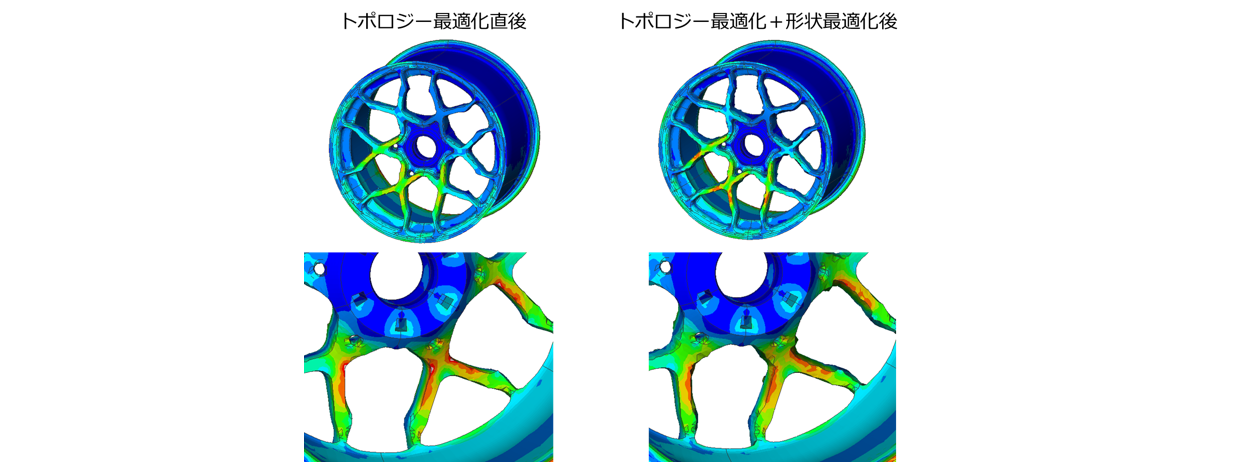
上図のトポロジー最適化最適化直後と形状最適化を実施した後の結果を比較すると、応力集中が緩和されてピーク応力が低下していることがわかります。
また、形状最適化後の方がスポークの応力分布が均一になっています。ホイールの疲労寿命向上に繋がる結果となりました。
以下にこのトポロジー最適化でのトピックをまとめます。

今回紹介したい代表的なトポロジー最適化のテクニックが上記です。その他にも使用した基本的なテクニックや、高度なテクニックには触れていません。(機会があれば紹介します)
特に重要なのが、3番と4番です。
3番:設定ミスに気付けたり、その製品のあるべき姿を理解することができます。
4番:トポロジー最適化は完璧ではありません。また、量産のために形状変更を加えた場合に要求仕様を満足できなくなることがあるためです。
ここで紹介したテクニックは、軽合金ホイールだけでなくCFRP製ホイールなど素材を選ばず利用可能です。もちろん、ホイール以外にも利用できるテクニックです。
↑GRMで開発したCFRP製ホイール(カーボンホイール)
以下余談です。
最適化結果に、「お気に入りの高性能ホイールに似た形状が無い!」と思われた方もいるかもしれませんが、スポーク形状(数や方向)を変えても、最終的な性能(剛性/強度/質量)は大きな差が出ません。もちろん、性能に差は出ますが、一般的なユーザーがブラインドテストで違いに気付くレベルではないと考えられます。(そうでなければ、ホイールメーカー各社のフラッグシップモデルは収斂進化の結果、同じ形状になってしまいますね)
つまり、「見た目がかっこいい!」「特定の使用用途に特化させたい!」など、他の要求からコンセプト形状を決定し、そのあとに様々な最適化方法を使用して要求性能を満足させることが可能です。
今回は、ホイールを題材にしてトポロジー最適化のテクニックを紹介しました。見たことあるな・・・という形状が多く見られ、ホイールメーカー各社の技術力の高さが窺い知れる結果となりました。
機能よりもデザイン優先で最適化するもの楽しそうです。3Dデータを支給していただければ事例紹介で最適化するので、試してみたい方はぜひご連絡下さい。